What makes Gantri sustainable?
A deep dive into our plant-based polymers
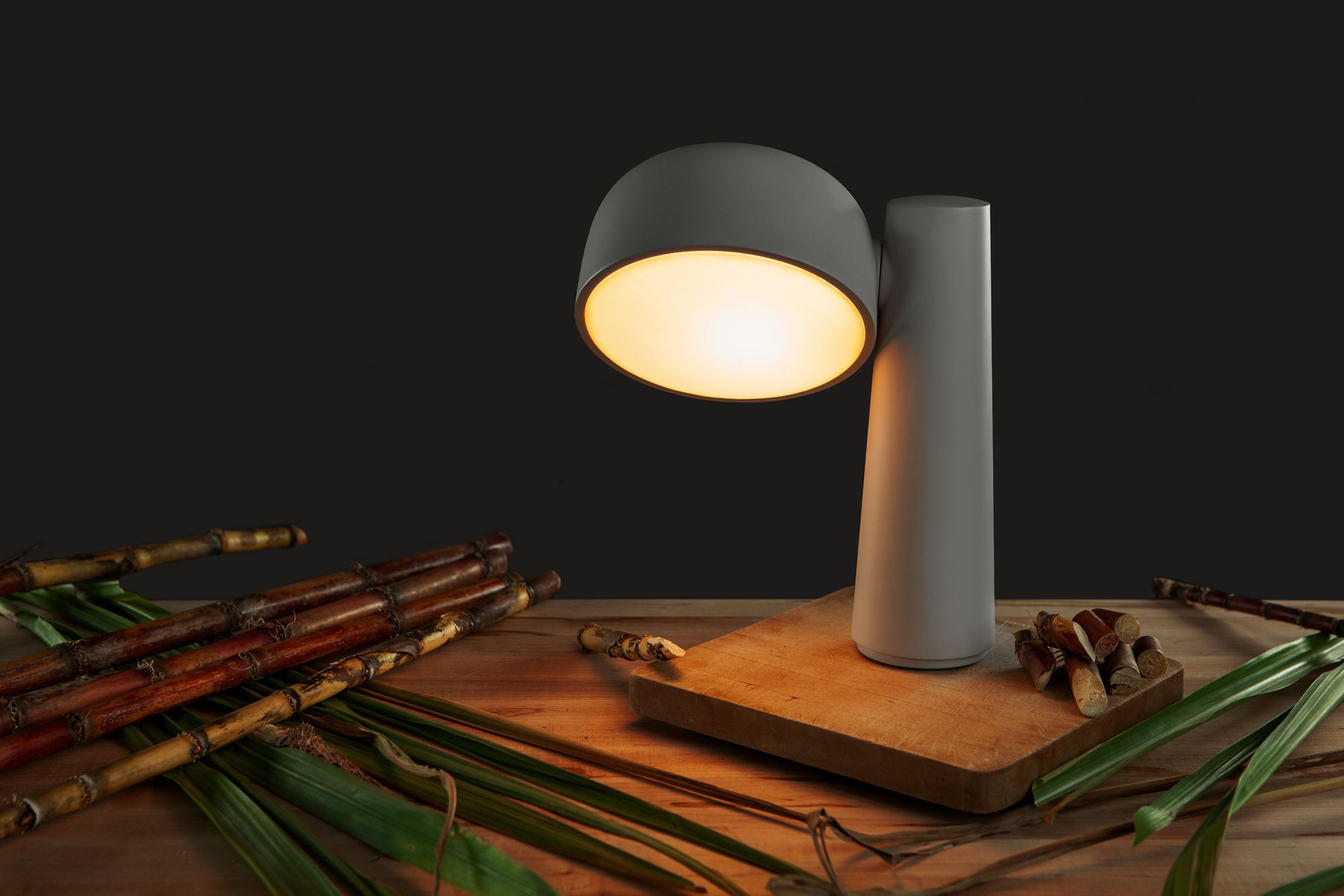

As we navigate a world where climate change is no longer theoretical, more people are looking for sustainable alternatives they can rely on. But what do sustainable products actually look like? This Earth Day, we’re breaking down how we approach sustainability at Gantri and how it all begins with our materials.
The problem with plastic
It’s no secret that traditional plastics are somewhat of a big bad wolf within the environmental conversation. They’re non-renewable, pollutive, and dangerous to manufacture. Not a good start for today’s climate.
The life of plastic begins with petroleum – a familiar fossil fuel foe. Not only is petroleum non-sustainable, it causes pollution at almost every stage of it’s journey to plastic-hood. When petroleum is drilled, there are risks of oil spillage, wildlife disruption, and water contamination. When petroleum is processed into plastic, harmful emissions are released into the air, sometimes putting entire communities at risk of health issues. Not to mention, the long term effects these emissions have on the climate at large. While petroleum-based plastic may be cheap and convenient, it’s impact is anything but.
Nature’s solution
From the start, we knew we wanted to make our lighting more sustainable and we searched far and wide for the perfect low-impact material. In partnership with colorFabb, we found a solution in the natural world. Uniquely derived from sugar crops, Gantri Plant Polymers are the world's first plant-derived polylactic acid (PLA) blends engineered specifically for premium lighting products. Unlike traditional petroleum-based plastics, our plant-based materials are safe, sustainable and most importantly - designed for beautiful lighting.
Plants > petroleum
When we evaluate how Gantri’s Plant Polymers compare to petroleum-based plastics, there are a few main benefits:
Lower impact: If traditional plastic production continues as usual, greenhouse gas emissions from plastic could reach 1.34 billion tons per year by 2030. Not only are these emissions a threat to climate change, they have dire effects on surrounding communities. We hope to slow down this trajectory with our plant-based polymers that produce 75% less CO2 per kilo, reducing our environmental footprint and encouraging safe manufacturing.
Renewable: The process of traditional plastics begins with distilling crude oils like petroleum. This practice is bad for the environment and it’s unsustainable. Fossil fuel based materials are finite – if we consume them for long enough, the resource will run out. Instead, we source our materials from non-GMO sugar crops such as corn, sugar beets and sugar cane. With sustainable farming, we can regrow our materials again and again.
Non-toxic: Plastic manufacturing as we know it can be hazardous. As heat and pressure are applied to the raw materials, toxic fumes are emitted. Fumes from plastics can irritate the lungs and are even thought to be cancer-causing. Our natural ingredients allow for safe manufacturing with no carcinogens emitted during production. No pollution, no harm.
Made for lights: Our polymers are engineered specifically for lighting. Our two custom PLA blends are created to be durable, heat tolerant and diffuse light evenly. Our diffusive blend offers a frosted glass-like effect while the opaque blend is finished with a premium, water-based paint. They are 50% more temperature resistant than traditional PLAs and safe to use near electronics.
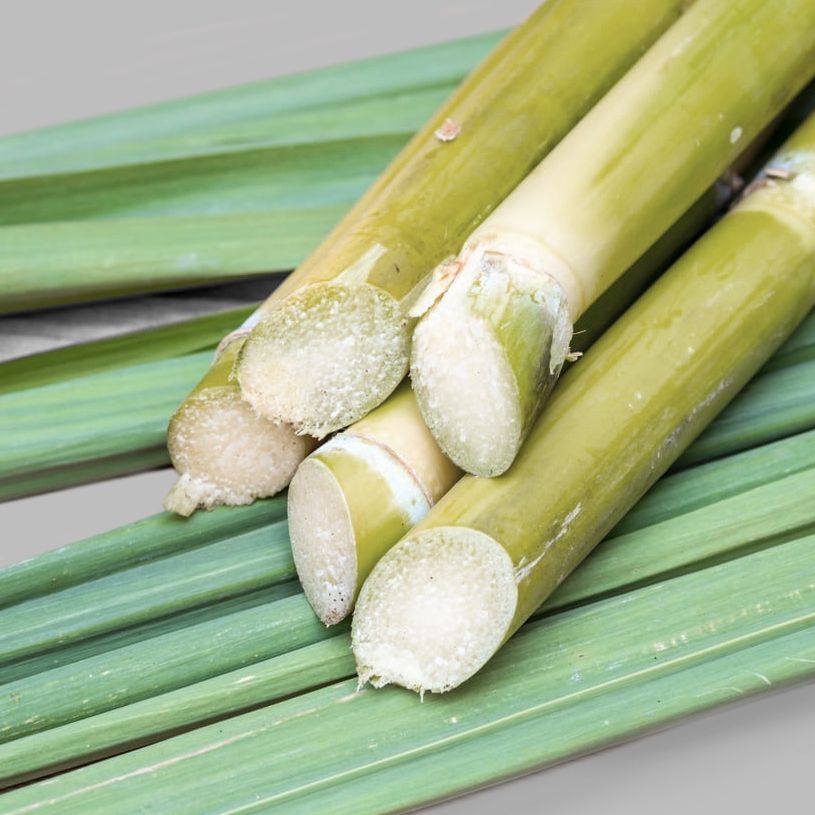
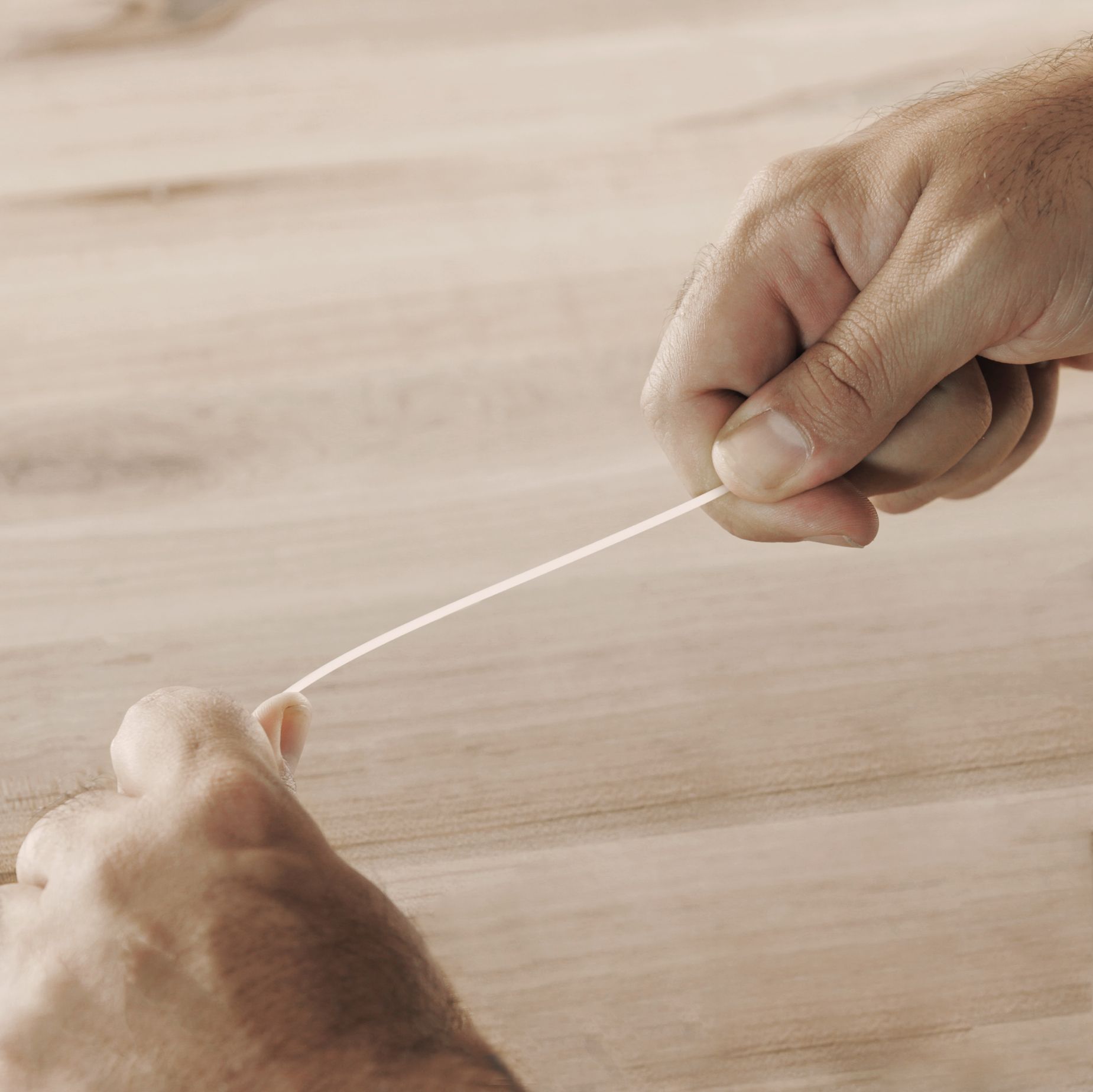
Our process
So how do sugar crops become a viable alternative to traditional plastic? Here’s a breakdown of how the magic happens:
Fermentation: Similar to winemaking, our sustainably sourced crops must go through a fermentation process. Large vats of sugar and starch solutions are inoculated with specific microorganisms. The solution sits in these vessels, termed bioreactors, for an extended period of time allowing fermentation to take place. Once the process is complete, lactic acid can be extracted for further processing.
Polymerization: Polymerization is the chemical process we leverage to create the base of Gantri Plant Polymers. The extracted lactic acid is joined by a catalyst to produce a chemical reaction. This reaction allows the lactic acid to form a molecular chain. The result is PLA, or polylactic acid.
Compounding: The pure PLA is then mixed with additives that serve a range of purposes. From increasing strength and durability, to altering opacity and improving printability – the additives work together to create our ideal polymer. Once the mixture is homogeneous, it is formed into pellets of compounded PLA.
Extrusion: The PLA pellets are fed into an extruder, where they’re heated and pushed through a tiny nozzle into thin strings of plastic called filament– think Play-Doh spaghetti. The extruded filament is cooled and wound onto large spools ready for printing.
When you order a light from Gantri, we feed the exact amount of filament needed from the spool to our 3D printers to create the product. When we make our lights to order, we reduce inventory waste and eliminate destructive practices commonly found in traditional manufacturing.

Our commitment
Beginning with our materials, Gantri is committed to sustainable manufacturing. Whenever we can, we use plant-based materials over artificial counterparts. Wherever we cannot, we use materials that can be recycled and reused. Lastly, we produce locally and on-demand, minimizing waste and shipping pollution.
“Gantri Plant Polymers are a reflection of our commitment to innovation and sustainability,” says Gantri founder and CEO, Ian Yang. “Our goal is to create great designs that you can feel good about. With our sustainable means of manufacturing, you can enjoy your new light knowing that it’s a better choice for the world.”