Combining Manufacturing and Sustainability Through Technology at Gantri
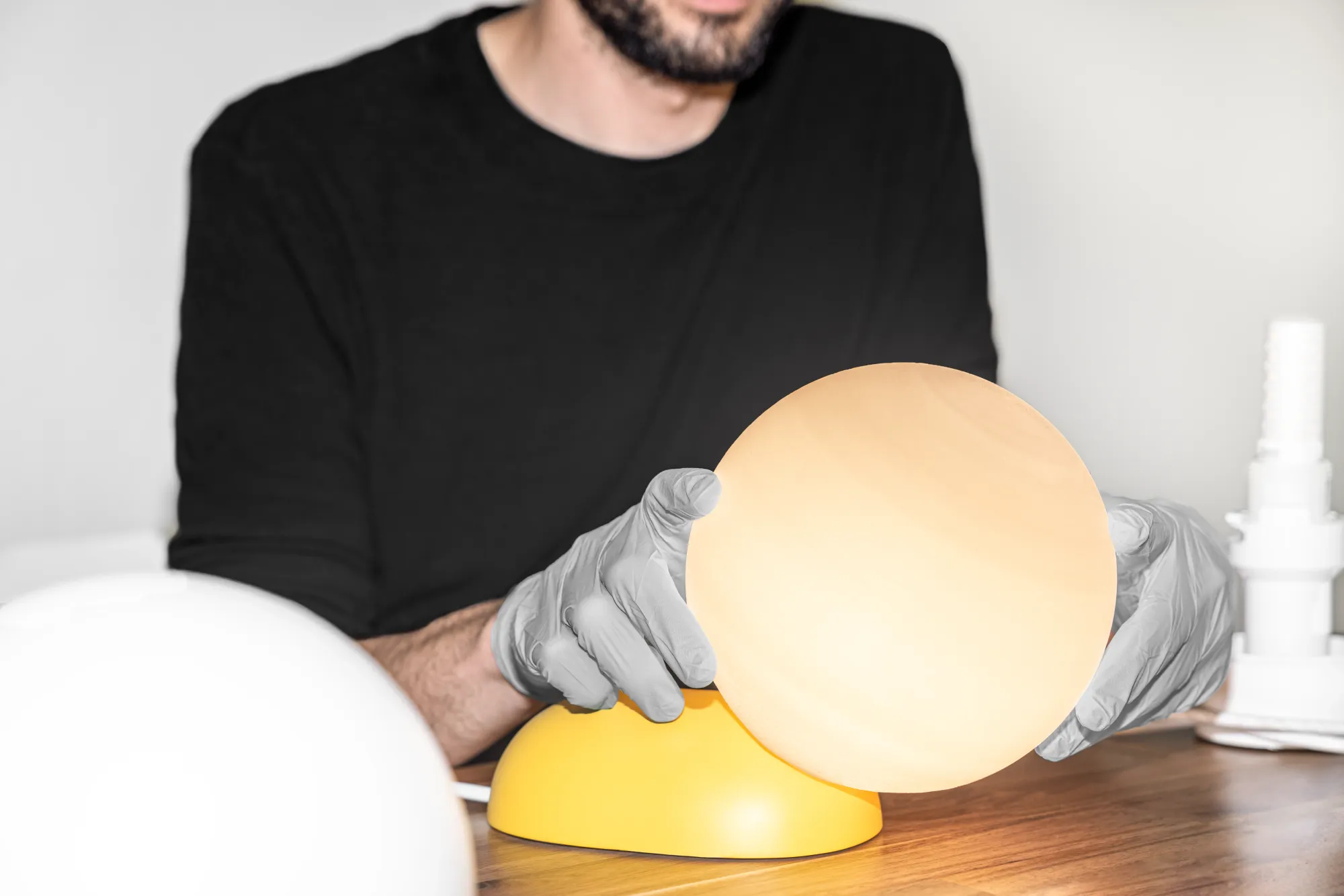
Here at Gantri, we pride ourselves on the steps we’ve taken to create an advanced and ecologically friendly production process derived from sustainable manufacturing technology. We’ve worked to reduce our environmental impact by lowering carbon emissions, minimizing waste, and conserving natural resources. We’re excited to share a peek behind the curtain to show our production steps—from the plants we use to create our signature Gantri Blend Polymers to the one-of-a-kind 3D printers that shape the components of our hand-assembled lights.
Biodegradable materials
There’s no single “secret” to Gantri’s eco-friendly approach to product design, but our Gantri Plant Polymer is a key ingredient to shaping a better future. You’ll be amazed how the bio-degradable material we use to construct our lights comes from just a few simple plants!
Meet Gantri Plant Polymers
First, a few definitions to clarify. A polymer is a substance composed of macromolecules. Macromolecules are composed of clusters of even simpler chemical units known as monomers. Polymers are frequently associated with human manufacturing: synthetic polymers such as nylon, Teflon, and other synthetic plastics. These synthetic materials are continuously manufactured and discarded.
While recycling efforts exist for some of these materials, they account for only a small fraction of the overall output. The waste places an ecological strain on our planet, not to mention the environmental impact of the CO2 released into our atmosphere during the manufacturing processes.
However, did you know that many polymers are naturally occurring? Polymers can be found in a majority of living organisms on our planet. Cellulose is a natural compound that creates the cell walls of green plants, supporting their physical structures. It is the most common organic polymer on Earth. Even collagen, which constructs the connective tissues in our bodies, is a biopolymer.
Humans have frequently utilized organic polymers throughout history. Cotton and paper were some of the first polymer innovations still in use today. More recently, biopolymers known as polylactic acid (PLA) have been implemented into 3D printing and consumer manufacturing to create more environmentally friendly products.
At Gantri, we use plant polymers derived from sugarcane and advanced sustainable manufacturing technology to maintain a carbon-neutral manufacturing process and eliminate excess waste, but how do we do it?
Sugar Cane and PLA
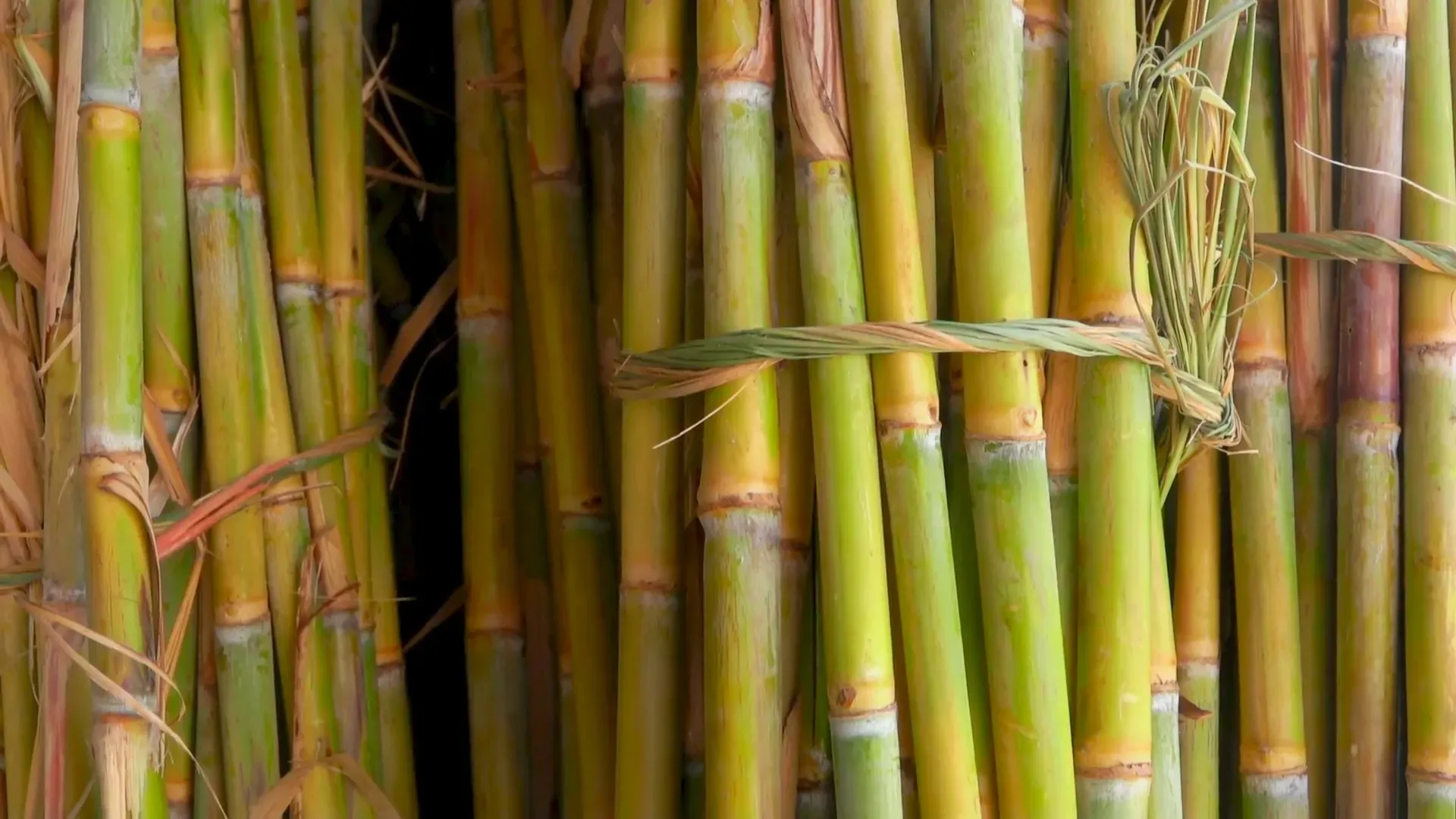
We utilize sugar cane as a renewable source of simple sugars and starch. As a GMO-free plant, sugar cane gives us a cleaner yield to extract the materials necessary for producing our eco-friendly products. Here’s our process for creating carbon-neutral manufacturing from these plants.
First, the sugar cane is sourced by our partners at ColorFabb. The sugar cane is farm-grown in Thailand in large quantities over multiple years using the same plant source. The raw cane is then harvested and ground to pulp during processing to extract simple sugar juice. The juice is then fermented using microorganisms to produce lactic acid from the sugar. This acid is dehydrated and transformed into long sequences of lactide monomers. Finally, these monomers are polymerized to create the polylactic acid used as the primary ingredient of Gantri’s Plant Polymer blends.
Waste reduction
After polymerization and compounding to create the signature Gantri Plant Polymer blend, we follow the golden rule of “measure twice, print once” to help reduce our production waste.
All our products begin their journey as tiny pellets of workable PLA material. These pellets are super-heated and squeezed into thin strings of printer-friendly filament. This filament is gathered in spools, and each individual product is carefully measured before printing. These accurate and precise measurements ensure that none of our eco-friendly materials are wasted during production.
Sustainable manufacturing processes
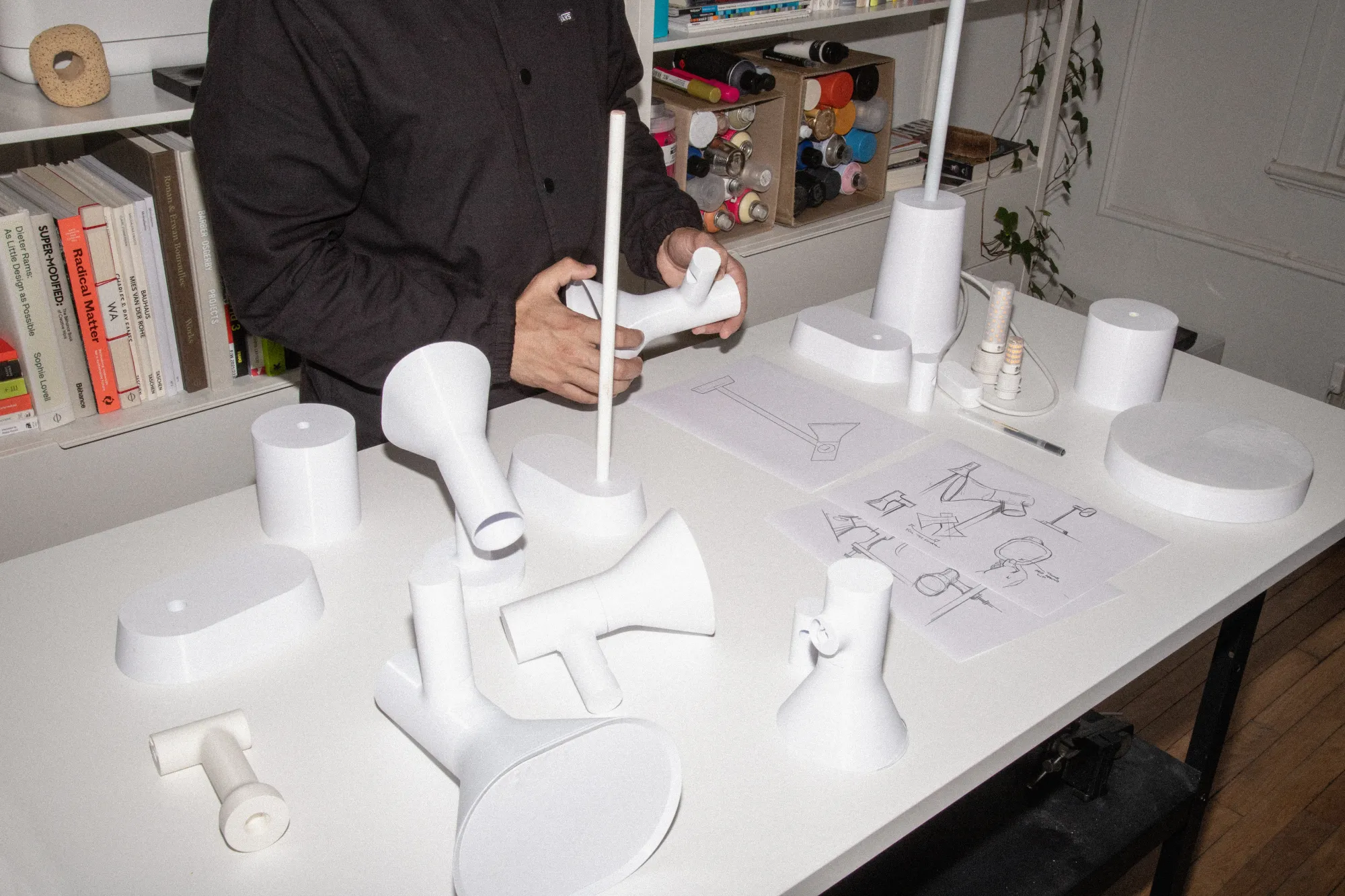
You may have heard about some of the leaps in advancement made in 3D printing technology, but did you know this sustainable manufacturing technology forms the backbone of Gantri’s product manufacturing? We’ve refined and innovated a truly one-of-a-kind digital process manufacturing ecosystem by upscaling the power of 3D printing to allow us to cater our entire product line to customers across the globe.
Our manufacturing process and factories are owned entirely by us so that we can tailor every step of production to ensure the highest quality products are created for our customers. This has been one of the biggest steps we’ve taken to reduce waste—streamlining production processes so our products are all made-to-order. This means we don’t have hundreds of our lights cluttering a warehouse somewhere wasting away and waiting to be purchased.
Energy efficiency
Gantri is always working to extend the technological efficiency of our products from the factory to consumers' homes across the globe. Here are a few ways our products are designed with energy efficiency in mind.
Efficiency from Production to Product
Advancements in energy efficiency start at the production stage here at Gantri. By utilizing the CO2 absorption of our excess sugar cane and the cleaner production of Gantri’s Plant Polymer mix, we are able to cut down manufacturing excess to produce 75% less CO2 per kilo compared to plastic production.
The LED Difference
Gantri uses only museum-quality LED light bulbs in all our products. It’s not just for the beautiful glow you can achieve with high-quality LEDs versus their incandescent counterparts. LED bulbs also use at least 75% less energy than any incandescent bulb. Plus, almost 90% of the energy used by incandescent bulbs is released as heat. This means that out of all the power they consume, an overwhelming majority is wasted.
Customers can also use our LED bulbs for much longer than standard incandescent or CFL bulbs. A longer-lasting bulb means fewer bulbs are trashed, which saves you money and produces far less waste in landfills across the globe.
Gantri brings aesthetics, manufacturing, and sustainability under one roof!
We hope you’ve enjoyed this dive into how Gantri marries sustainability and manufacturing with technology and clever design to create eco-friendly products for everyone to enjoy. One of the best things an individual can do to reduce their own carbon footprint is to support ethical retailers and sustainable products.
When cutting-edge lighting solutions are purchased from our shop, the customer can be assured they are not just receiving a glowing work of art from the minds of one of our designers. They can also have peace of mind that their product has been ethically sourced and intelligently designed, all with groundbreaking advancements to reduce ecological impact. All this work comes together for that first enchanting moment you turn on one of our lights and experience the Gantri difference.